This is an amazing country, rich in beauty and all of us carry the responsibility of keeping it that way. When we in the industry consider our environmental impact, not just in our own country but globally we have to consider our collision repair centres, industrial manufacturers, commercial painters and everyone whom own a spray painting booth.
A simple and easy way to protect the protect the environment is to properly dispose of your paint booth exhaust filters.
It is also just as important to regularly change your exhaust filters at the correct interval, use OEM approved paint booth filters and of course disposal of them in the correct manner according to your local state or national authority.
By doing this you are not only ensures your business is following the law, but it is also what is best for the environment.
One day we hope it will be possible to recycle exhaust filters, however currently this is not a viable option in Australia.
So with this said we would highly recommend the following steps be followed in accordance with your local state and municipality specific requirements.
Here are five steps for proper exhaust paint booth filter disposal:





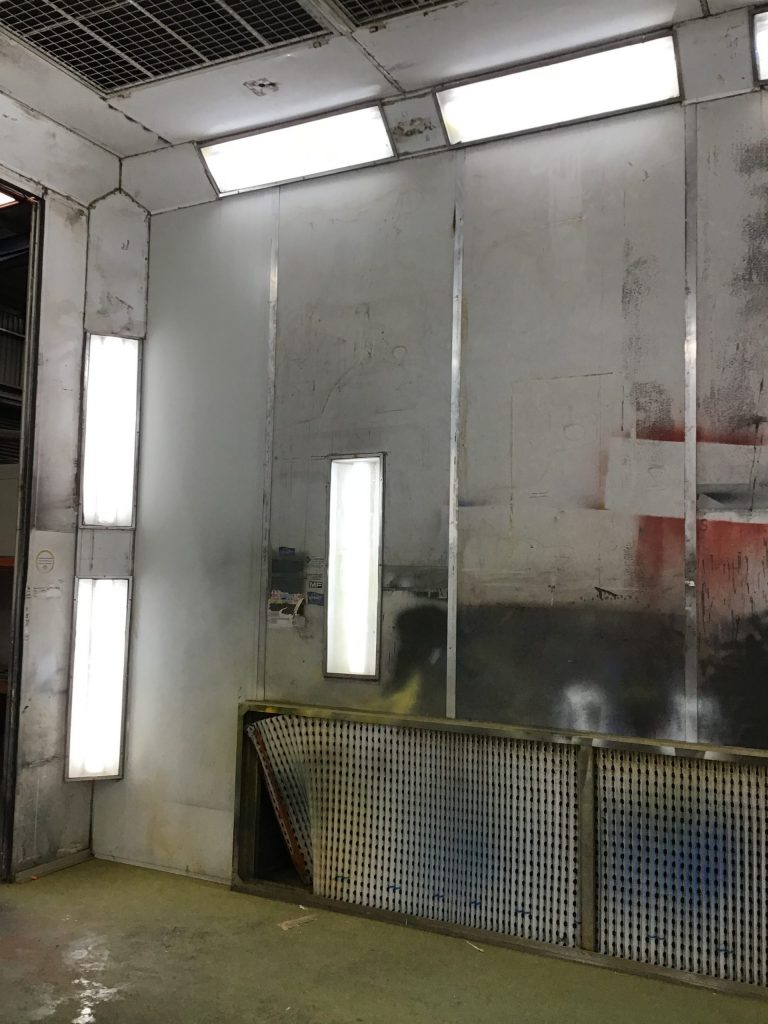
STEP 1: Understand what paint type of paint is being captured by your spray booth exhaust and if these paints are hazardous in nature
We always recommend referring to your paint suppliers MSD’s sheet first and foremost. The MSDS from your paint supplier will identify what types compounds or chemicals are in your paint and if these are hazardous or not.
So before disposing of your paint booth exhaust filters as general waste, you need to verify your filters have not been exposed to any of the hazardous compounds can be found in various paints commonly used in industrial or commercial spray paints.
You must assess and classify your waste in accordance with the Australian, the attached download link from the environmental standards will help you do this ENVIRONMENTAL STANDARDS (DOWNLOAD) ASSESSMENT AND CLASSIFICATION OF LIQUID AND NON-LIQUID WASTES
You may need to engage a specialist lab to test your water material if you are unsure of how to determine if the paint you sprayed contains specific compounds.
While the document from the Environmental Standards does nominate fully cured and dried residues of resins, glues, paints, coatings and inks as General solid waste (non-putrescible) this does not include paints that would be classified to contain hazardous compounds at all or in specific quantities based on the hazardous assessment of the paint product.
For example your filters would likely be considered hazardous if a certain amount of any of the following compounds are present in your filters:
- Arsenic
- Benzene
- Benzo(a)pyrene2
- Cadmium
- Chromium
- Please refer to full list in the attached link.
It is noteworthy to consider that this information specifically applies to your spray booths exhaust filters. When we consider your supply air or spray booth inlet filters, these filters are designed to remove dust and other small airborne particles from the atmosphere (outside) your building. They are designed to supply a contaminant-free environment for enclosed spray-painting booth.
Therefore if your intake filters have not come in contact with paint in any way then they would be considered to be not hazardous. As such we would suggest that by meeting this criterion your intake filters can be disposed of in your normal trash.
STEP 2. Correctly Dispose of Hazardous Paint Booth Exhaust Filters in line with Australian Standards when hazardous.
If you have identified your paint booth exhaust filters to be deemed as hazardous then these filters cannot be disposed of as general or standard waste.
The exhaust filters must be dry, paint within the filters must be fully cured before any storage or disposal occurs to reduce ignitability. This is of course unless you are dealing with a water filtration spray booth which is a separate topic completely.
Your responsibility for dry exhaust filters is to correctly store these filters in a clearly sealed and marked container to ensure that no leakage of the hazardous compound could occur. Typically, this storage could be inside of a 44-gallon drum or equivalent style of container. It must also be clearly marked as hazardous waste and the MSDS sheet or evaluation document for the hazardous substance be attached.
Once correctly sealed we suggest you contact and use a licensed hazardous waste transporter to pick up the container and drop off to an approved hazardous waste disposal facility where a disposal certificate can be supplied (if applicable)
STEP 3: Housekeeping process for painters – Do not to blow out spray guns with paint, thinners or gun cleaners into the Paint Booth Exhaust Filters.
This is critical, we see so many painters get this wrong. Leading to a number of paint transfer problems (carry over) past the filters and as such ending up on your spray booth motors and throughout ductwork. Not only does this reduce your spray booths performance and safety it also contaminates your filters with hazardous solvents that effect the classification of your filters.
When cleaning your spray gun, make sure to keep solvents away from the paint booth filters.
It is best to spray solvents into closable hazardous waste collection containers or use a gun washing system where solvents can be recycled and collected correctly
STEP 4: Check before you dispose – you must contact the waste disposal company before Disposing of Non-Hazardous paint booth exhaust filters
It is important to always consult and inform your waste supplier before they pick up any spray booth filters. Just let them know, even if your paint booth exhaust filters are not deemed to be hazardous waste, by notifying your waste management company that you are disposing of the filters as standard waste you are able to confirm if they have any special requirements before pick up.
Your waste management company could ask you to provide proof that no hazardous compounds are present in the filters, so it’s best to be prepared with your MSDS sheets and evaluation documents if they apply.
By doing the above as a continuous process you will be able to be confident in your business’s waste management. We recommend continuous improvement and evaluation to make sure your requirements are being kept up to date.
Important note:
Within this article we are providing a general framework to help the industry better understand what a good process of exhaust filter waste management would look like. It is important to remember that regulations regarding spray booth exhaust filter disposal vary from state to state and Australian regulations are constantly evolving to ensure best practices are met. We suggest engaging with your suppliers and your local authorities so they can tell you the requirements specifically for your area.
We ask that everyone always considers the environment and the impact that general and hazardous waste has on the way we live and operate.